Introducción
Las torres de refrigeración son elementos esenciales en muchas instalaciones de procesos industriales, y su correcto funcionamiento es crucial. Dentro de estas torres, hay varias piezas de maquinaria rotativa, como lo son motores, cajas de engranajes, ventiladores y ejes. Esta maquinaria requiere un monitoreo constante de las vibraciones para prevenir fallas y averías catastróficas, ya que estas fallas pueden provocar pérdidas en la producción, riesgos para la seguridad y costosas reparaciones, las cuales pueden retrasar una planta durante meses. En este artículo de blog, analizaremos cómo la tecnología de sensores Wilcoxon ayuda a mantener el funcionamiento óptimo de las torres de refrigeración en una instalación de procesamiento de gas natural en las afueras de Chicago, Illinois, al mismo tiempo que se reducen los costos.
Parte I: Identificación y Solución de Problemas en los Motores
Aux Sable, una planta de procesamiento de gas natural en las afueras de Chicago, ha experimentado los beneficios del monitoreo de vibraciones en su maquinaria crítica durante años. Desde 2001, Aux Sable ha monitoreado los componentes de sus torres de refrigeración con acelerómetros de Wilcoxon Sensing Technologies.
El modelo 797 de Wilcoxon, un acelerómetro estándar de salida de 100 mV/g, se montó en el extremo de accionamiento (DE) de un motor acoplado directamente a un ventilador de una torre de refrigeración de Aux Sable. El motor funcionaba a dos velocidades diferentes, 1790 y 893 RPM. Durante un periodo de tres años, de 2004 a 2006, el sensor registró un aumento general de las vibraciones de 0,07 ips pico a 0,19 ips pico, siendo ips las pulgadas por segundo. Aunque el nivel de vibración no activó una alarma (ya que esta se fijó en 0,20 ips pico) el aumento combinado con un ruido audible procedente del motor despertó el interés de Aux Sable.
Al investigar el problema en el DE del motor, el análisis espectral de la señal de vibración medida mostró un defecto, el cual se localizaba en el cojinete del extremo no motriz (NDE) del motor, concretamente en la pista interior (BPFI).
Con este análisis, Aux Sable decidió retirar el motor defectuoso en noviembre de 2006 y sustituirlo por uno de repuesto. El proceso se completó durante una parada planificada y el motor se envió a un taller de reparación para su inspección. Como indicaba el análisis de vibraciones, la inspección confirmó el defecto del cojinete del extremo no motriz del motor, y la causa era el aumento general de las vibraciones.
En la foto de la derecha se aprecia el defecto en la pista interior de los cojinetes NDE del motor. La pista exterior, que se ve en la foto inferior derecha, mostraba óxido y corrosión causados por un ajuste inadecuado del rodamiento a la carcasa.
El taller mecánico pudo reparar el motor en menos de un mes, por menos de 5.000 dólares. Una fracción del presupuesto de 20.000 dólares para comprar un motor de respuesto con un plazo de entrega de 10 semanas. El técnico que realizó la reparación señaló que el motor no habría durado mucho más antes de que se produjera un fallo catastrófico, que además podría haber dañado al ventilador acoplado y provocar una parada imprevista o una redución del rendimiento.
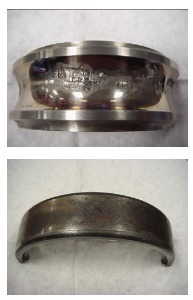
Parte II: Rectificación de la Caja de Engranajes
Después de resolver el problema de los cojinetes del motor en noviembre de 2006, Aux Sable amplió su programa de control de vibraciones para incluir las cajas de engranajes de los ventiladores de las torres de refrigeración. Montaron acelerómetros Wilcoxon en cada caja de engranajes e instalaron cables desde los sensores hasta una carcasa de Wilcoxon montada fuera de la carcasa del ventilador para una cómoda toma de datos.
Cada caja de engranajes se monitorizó en el eje de entrada, con velocidades de 29,83 y 14,91 Hz, y el eje de salida, que giró a velocidades de 2,13 y 1,06 Hz. El 797L de Wilcoxon, con una sensibilidad de 500 mV/g, se diseñó específicamente para bajas frecuencias y se utilizó para controlar las bajas velocidades de rotación del eje de salida.
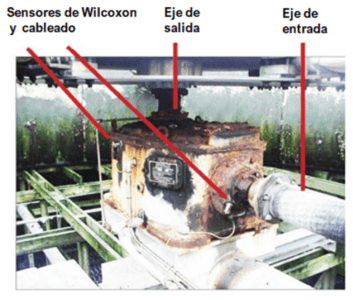
Los datos de las vibraciones se recogieron mensualmente de las carcasas y fueron analizados por los técnicos. En octubre de 2008, la tendencia de las vibraciones mostró un gran aumento y activó un nivel de alerta preprogramado. Agregado al análisis del aceite de meses antes, que indicaba un desgaste anormal en los cojinetes de la caja de engranajes, el análisis de vibraciones mostró un defecto en el cojinete inferior del eje de salida de la caja de engranajes. La caja de engranajes se sustituyó durante una parada planificada, y allí fue que una inspección del cojinete confirmó lo que los sensores habían estado midiendo.
La imagen de la derecha muestra una fatiga del metal. Casi el 60% de la pista de rodadura exterior se había erosionado. Los 21 rodillos cónicos del cojinete inferior del eje de salida y la pista interior del eje de salida mostraban severos daños por corrosión.
Debido a que el monitoreo de vibraciones activó un aviso antes de que de que la caja de engranajes llegara a un fallo catastrófico, sólo hubo que sustituir los cojinetes y las juntas. Todos los demás componentes principales de la caja de engranajes, incluidos los engranajes, estaban en buen estado. Los costos de reparación ascendieron a algo menos de 2.700 dólares, mientras que una reconstrucción habría costado más de 13.000 dólares. Además, si la caja de engranajes hubiera funcionado hasta fallar y no se hubiera sustituido durante una parada planificada, el tiempo de inactividad imprevisto del ventilador y la reducción de agua de refrigeración podría haber causado una pérdida de productividad durante una demanda pico.
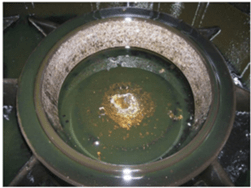
Parte III: Nuevas Cajas de Engranajes e indicadores para Monitoreo Continuo de Vibraciones
Entre enero y noviembre de 2012, las tendencias de un sensor Wilcoxon mostraron un aumento general de las vibraciones de 0,10 ips pico a 0,24 ips pico. El análisis del aceite mostró que el nivel de aceite era normal y no estaba relacionado con el aumento de las vibraciones.
El análisis de vibraciones indicó un pico de amplitud en la frecuencia de engrane de 269 Hz. Los gráficos siguientes representan los datos espectrales de los sensores de vibración en toda la gama de frecuencias (izquierda) y el espectro problemático ampliado (derecha). El espectro ampliado muestra numerosas frecuencias de banda lateral a intervalos de 4,5 Hz, asociadas a la velocidad intermedia del eje de la caja de engranajes. La amplitud era aproximadamente el 30% de la frecuencia fundamental, un nivel de gravedad moderado.
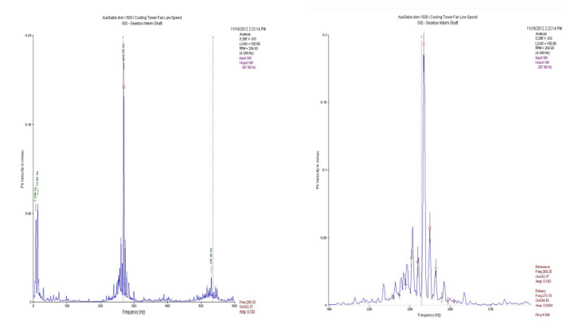
Un gráfico en cascada seguido a lo largo del año mostraba un aumento continuo de las amplitudes tanto de la frecuencia de engrane como de las bandas laterales. La caja de engranajes se sustituyó por una de repuesto en la primera oportunidad y se efectuaron reparaciones.
Parte IV: Supervisión de Entornos Extremos
Tras más de 10 años de funcionamiento en la torre de refrigeración y sometidos a ácido sulfúrico, agua pulverizada, suciedad y mugre, los sensores fueron desinstalados y reemplazados. La imagen de abajo muestra los dos sensores que salieron de la caja de engranajes en 2012. El sensor de la izquierda ha sido limpiado de la mayoría de los contaminantes, mientras que el sensor de la derecha está igual que cuando se retiró de la caja de engranajes. A pesar del entorno duro, húmedo y corrosivo, ambos sensores han funcionado igual que en el momento de la puesta en marcha.
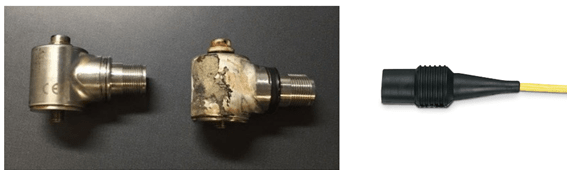
En combinación con el conector tipo bota R6Q(I) y el cable J9T2A con revestimiento de teflón, como se ve en la imagen de la derecha, los contaminantes no penetraron el cableado eléctrico y la señal se mantuvo clara durante toda la vida útil del sensor.
Con los duraderos sensores, cables y carcasas de Wilcoxon, y la experiencia en análisis de vibraciones de Aux Sable, la empresa ha evitado varios fallos catastróficos, daños en los equipos acoplados y paradas imprevistas, para mantener operativas sus torres de refrigeración. Aux Sable sigue creciendo, extrayendo combustible líquido del gas natural en todo Canadá y el norte de Estados Unidos.
Conclusión
El monitoreo de vibraciones es un componente esencial en el mantenimiento de las torres de refrigeración y sus maquinarias asociadas. La implementación de sensores Wilcoxon en Aux Sable ha demostrado ser una solución eficaz y rentable para prevenir fallas catastróficas y costosas reparaciones. La inversión en tecnología de monitoreo y análisis de vibraciones es una decisión inteligente para cualquier empresa que busque mantener un rendimiento óptimo y evitar pérdidas innecesarias.